製造現場プラットフォーム「TULIP」(チューリップ)の活用が拡大しているDMG森精機。すでに700以上のステーション(※)が稼働し、生産・品質管理・点検など広範に活用されています。
さらにTULIPを物流面の改善につなげる取り組みが進んでおり、今回はその中から「フォークリフト運行状況見える化」の実現について紹介します。
※ステーション:製造ラインや作業場所等に配置する端末の単位を指します。TULIPのライセンスはステーションごととなります。
この記事のポイント●状況の見える化
フォークリフトの使用状況をタブレットから見える化し、確認のためのムダな歩行を排除
●業務の見える化
記録するだけの日報から、WF化し、報・連・相が円滑に行える仕組みに改善
●データ活用による業務改善
集計データを分析し、フォークリフト専任者に業務を集約することで全体最適化
手間に感じながらも目視と紙の日報でフォークリフトを使用
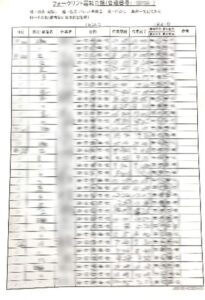
紙で管理していた運転日報
DMG森精機伊賀事業所内の主軸工場加工エリアにはフォークリフトが1台常設されており、改善前は以下のような流れで使用していました。
フォークリフト使用の流れ(TULIP導入前)
・待機場に行き、使用されていなければ(待機場にあれば)使用
・フォークリフトを待機場に戻し、運転日報に使用者氏名、使用開始・終了日時などの必要事項を記入して完了
この手順には大きく2点、課題がありました。
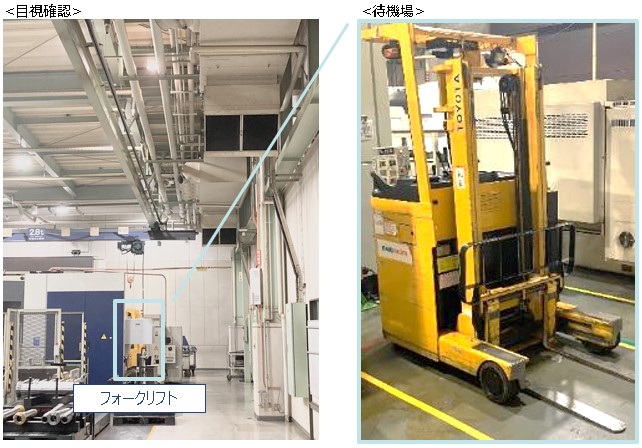
フォークリフト待機場そばまで行き目視確認を行っていた
まず、行ってみるまですぐ使えるかわからない点。
エリア内の配置上、待機場そばの通路まで行かないとフォークリフトがあるか目視できず、使用中だった場合には何度も確認しに行く必要がありました。
もう1点は運転日報の運用・管理。
A4サイズの用紙に印刷された表に手書きで記入しており、作業内容や時間があいまいだったり、汚くて読めなかったりという状況でした。
そして記入された情報は活用されず、用紙を保存するだけになっていました。
そのほか、作業中にフォークリフトに傷などの異常が見つかった場合には運転日報に記入していましたが、詳細を記載するための十分なスペースはなく、正しく情報が伝わらないこともありました。
TULIP化で課題解決へ
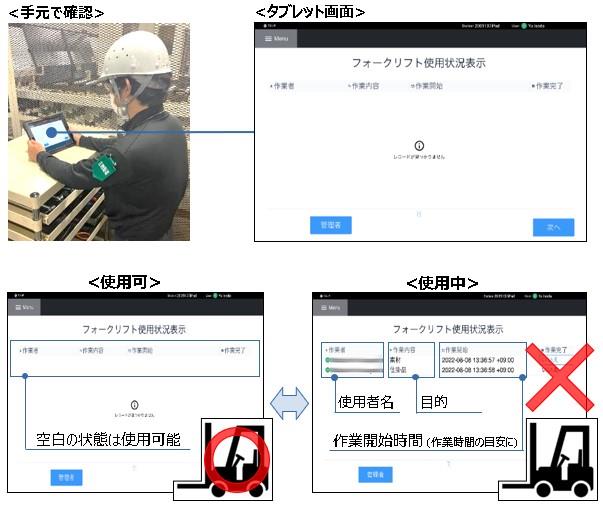
TULIPでフォークリフトの使用状況を確認
点検記録簿などと同様に、運転日報をTULIP化することで課題解決を図れると考えTULIPアプリを作成、運用を開始しました。
TULIPはアプリ作成数の制限がないため、新しい試みにも気軽にチャレンジできます。
運転日報をTULIP化することで手書きは当然不要となり、作業内容も選択式にし、入力の手間削減と分析のしやすさを向上させました。
社員番号をQRで読み取り、作業内容を選択し、開始・終了ボタンを押すだけで使用時間が自動集計され、かつ使用状況をスマートフォン・タブレットから簡単に確認できるため、非常に効率が良くなりました。
また、作業終了時にフォークリフトに傷などの異常が見つかった場合は、タブレットで写真を撮影して関係者に自動でメール配信を行うフローにして、客観的な情報を簡単・確実に伝えられるようになりました。
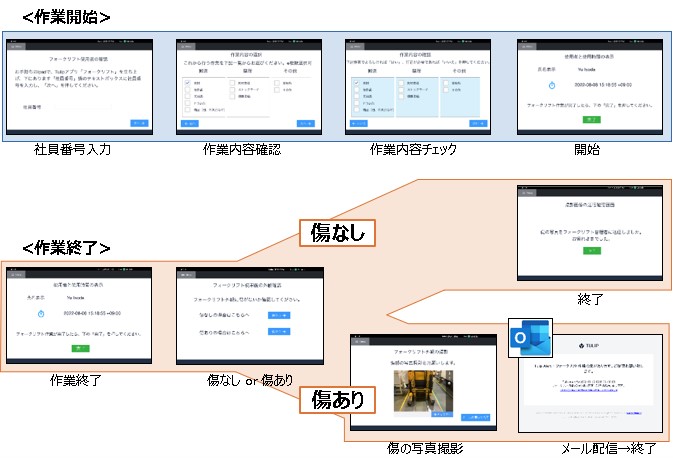
TULIPでの入力フロー
集計データを分析し、フォークリフト使用の仕組みを改善
運転日報をTULIP化することで、あいまいだった使用状況を詳細・正確に取得でき、集計も自動で行えるようになりました。
1日の稼働時間は約4時間、曜日によるばらつきは小さく毎日確実に使用されています。また、月に20人以上がフォークリフトを運転しており、数分しか使用しない作業者も複数名いるという結果でした。
こうしたTULIP化で得られたデータをもとに、「各自が運転する仕組み」から「専任の作業者に集約する仕組み」に変更しました。
専任化することで工場全体の物流業務の効率を向上できること、また運搬業務を集約することで、多くの作業者をより付加価値の高い業務に集中させられることが判ったためです。
TULIPはPDCASサイクル を加速・最適化する
製造業のIoTプラットフォーム
紙のチェックシートのような手書きが介在する業務を、まずTULIPでデジタル化すると、今まで見過ごしていた異常値や不具合を抽出しやすくなり、業務プロセスの改善が進みやすくなります。
改善された業務プロセスを新たな作業標準としてSDCAを回し、また新たな改善点が見付かればPDCAを回して改善していく。PDCAに標準化(Standardization)を加えた「PDCAS」サイクルの実現に寄与するサービスとして、TULIPは製造業の皆様にご評価いただいています。
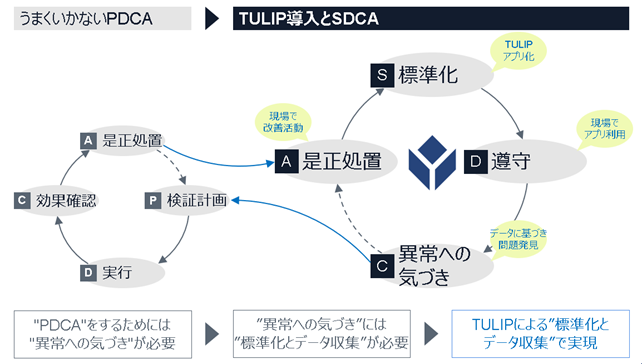
TULIPでのPDCASサイクル
DMG森精機株式会社URL
https://www.dmgmori.co.jp/
※掲載内容は原稿掲載時のものです。