今回はマツヤ産業株式会社 伊賀事業所長 市耒様にお話を伺い、カシメ忘れの不具合を未然に防ぐポカヨケシステムを自社の担当者自ら構築した事例を紹介します。
ポイント◦ 不具合対策を二重三重チェックで対処するのではなく、システムによる自動チェックを実現
◦ プログラミング経験のない自社担当者がシステム開発。業務フロー変更にも社内で即対応可能
◦ 業務を理解している現場主導の開発により、必要十分なシステムを短期・安価で構築
作業者の目視頼み…カシメ忘れ発生リスクをなくしたい!
潤滑パイプの製造工程でのカシメ(※)作業では、カシメ後に目視で確認を行っていました。
しかし作業者の確認ミスなどからカシメ忘れが発生するリスクは認識しており、TULIPで改善を図ることにしました。システム化までの手順は次の通りです。
※カシメ:溶接・接着剤・ねじ・ボルトを使わずに金属同士を締結できる加工方法の総称。
今回は鋼管と継ぎ手の隙間から液体が漏れないようにカシメを行っている。
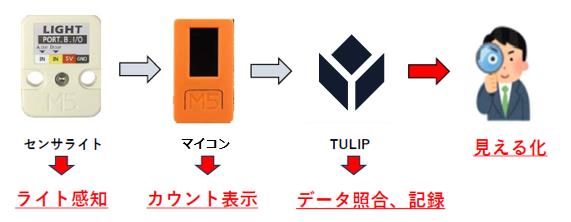
システム構成の全体イメージ
1. 図面を含めた作業手順をTULIPアプリ化する
アプリ化により、カシメ箇所を含めた図面上の様々な情報をデータとして保持できるようになります。TULIPでのアプリ作成は、プログラミングの経験がなくともプレゼンソフトで資料を作るように行えます。
2. カシメ完了のランプ点灯を認識させる
カシメについては、カシメ機のシリンダにあるLED点灯ごとに完了と判断することにしました。
シリンダの動きなど実動作の利用も考えましたが、仕組みとして複雑で規模も大きくなってしまいがちです。間接的に判断できるLED点灯で目的は十分果たせるだろうということで、点灯を感知する一般的なセンサ(※)をLEDの近くに設置しました。
※M5Stack Technology社の光センサユニットを使用
3. ランプ点灯をカウントする
感知した点灯情報は、センサとM5StickC Plusというマイコンを接続してカウントし、TULIPへ転送する仕組みを作りました。
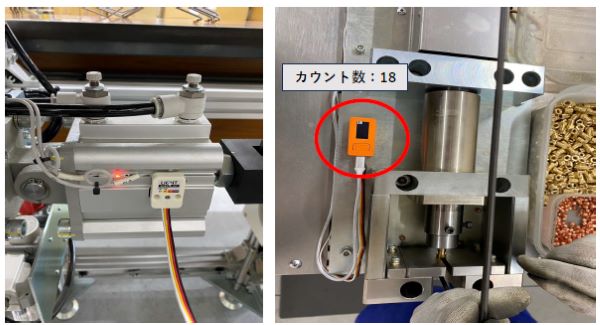
カシメ機に取り付けたセンサ。カシメ回数がカウントされる
4. 点灯回数とカシメ回数を照合、合致する場合のみ合格とする
TULIPで保持している図面ごとのカシメ回数の情報と、ランプ点灯で取得した実際のカシメ回数とを照合、合致する場合に合格として記録を行います。
自動で記録まで行えるので、工数削減はもちろん、記載ミス・確認ミスを撲滅でき、実績をデータとして保存・確認できるようになりました。
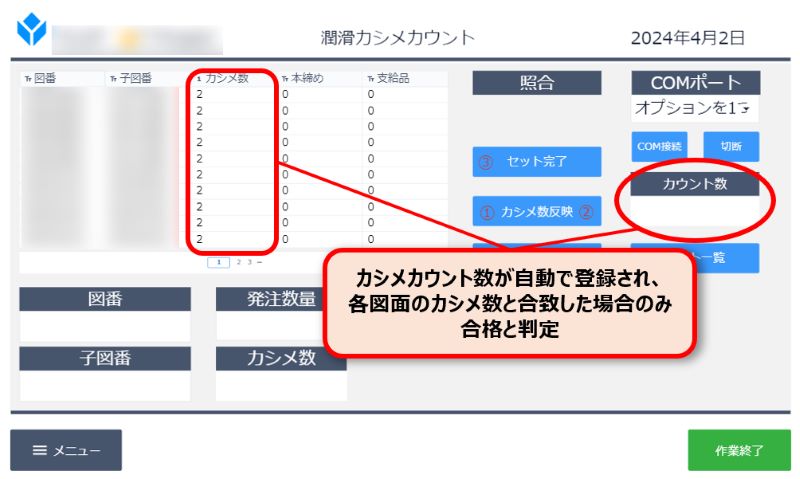
TULIPアプリ画面。カシメカウントが登録され合否判断まで自動化
導入にかかった期間は3週間ほど、費用も実費で5千円ほどと、非常に安価・短期間でカシメ回数のカウントと照合の自動化を実現できました。
社内で不具合対策の仕組みを構築できるのは、TULIPならでは。今後業務手順が変わったりしても、業務に合わせて社内で仕組みをアップデートできます。
1924年 (大正13年)創業の歴史ある企業ですが、近年は工作機械用APC (自動パレット交換装置)等の部品加工・組立も行っており、事業とノウハウをますます拡大しています。
DXにも早くから取り組んでいるマツヤ産業株式会社では、製造現場DXプラットフォーム「TULIP」を2020年から導入。複数の組立工程に活用して新入社員の教育期間を1/3に短縮するなど効果を上げてきました。
プログラミング知識がなくても作業者や管理者が自ら業務アプリケーションを作成・改善できるTULIPの特長を活かし、今回ご紹介したように同社での活用範囲が広がっています。
マツヤ産業株式会社Webサイト:https://www.matsuya-ind.co.jp/
手順が明確になることで業務の標準化も同時に実現され、スキルによる確認レベルの差もなくなるため教育コストの大幅削減にもつながります。
※掲載内容は取材時のものです。
※記事内画像はマツヤ産業株式会社様資料より引用・作成。
※M5StickC PlusはM5Stack Technology Co., Ltdの商標または登録商標です。